FUJI ELECTRIC, ALPHA 7 SERIES SERVO SYSTEM
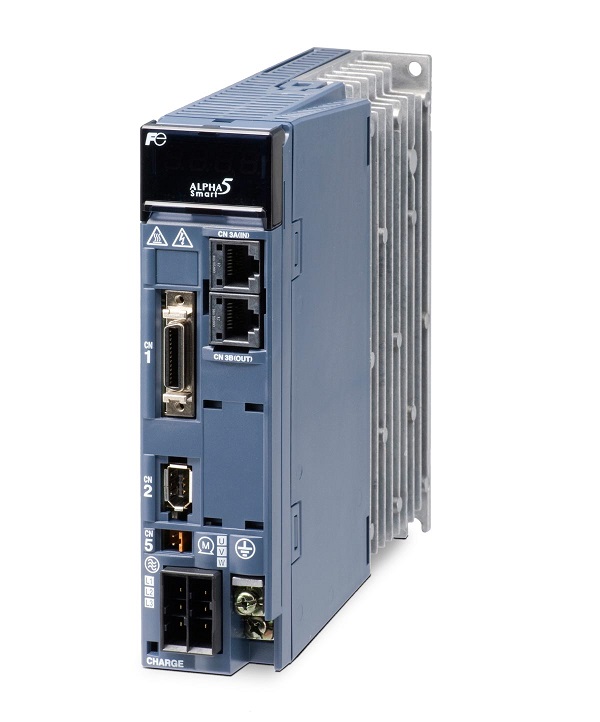
- Speed and frequency response at 3.2kHz realizes ultra-high-speed control
- Maximum instantaneous torque of 350%* enables response to high-speed commands
- The 24-bit fine resolution INC/ABS encoder significantly improves the precision of control
- Safer operations are ensured by various safety functions
- Transparent communication allows you to configure multiple amplifiers from a single central location.
FUJI ELECTRIC, ALPHA 7 SERIES SERVO SYSTEM
Speed and frequency response at 3.2kHz realizes ultra-high-speed control.
Fuji's proprietary control algorithm achieves a speed and frequency response at 3.2kHz, the highest level in the industry. This reduces the tact time, enabling high-speed control.
Maximum instantaneous torque of 350%* enables response to high-speed commands.
The maximum instantaneous torque of the servo motor is now as high as 350%.
* This is applicable only to certain models.
The 24-bit fine resolution INC/ABS encoder significantly improves the precision of control.
The encoder resolution is now as high as 24 bits. This provides much higher control precision than before, enabling high-precision control.
Fuji Electric Alpha 7 Safer operations are ensured by various safety functions.
Standard equipment includes the STO function defined in the international standard IEC61800-5-2. In addition, the WSU-ST1 option adds support for SS1, SLS, SBC, and SSM. These safety functions can be easily configured with parameters.
Equipped as standard with STO (Safe Torque Off).Upon receiving an input signal from external equipment, the servo system shuts off the output from the servo amplifier and enters into free-run mode.
Support for SS1 (Safe Stop 1) *Option.
Receiving an input signal from external equipment, the servo system operates the STO function when the speed is reduced to the specified value or the specified period of time elapses.
Support for SLS (Safely Limited Speed) *Option.
The servo system monitors whether or not the speed limit value is exceeded and, if exceeded, enters into STO mode.
Support for SSM (Safe Speed Monitor) *Option.
The servo system outputs the SSM signal when the specified speed is exceeded.
Support for SBC (Safe Brake Control) *Option.
The SBC signal is an output signal for controlling an external brake and operates synchronously with STO.
Maximize Fuji Electric Alpha 7 performance by using MICREX-SX in conjunction.
You can use the transparent communication feature to configure the parameters of multiple servo amplifiers from a single PC via the motion controller. In addition, connection with Fuji's MONITOUCH allows Wi-Fi communications with servo amplifiers.
A single CPU performs both sequence and motion control.
Adding a single unit of MICREXSX eliminates the need of a module dedicated to motion control, thus significantly reducing the initial cost. Also, work efficiency is dramatically improved by supporting both sequence and motion with a single programming tool.
Directly connectable with a single SX bus and easy to wire and extend.
Just a single bus cable completes the connection between the controller and servo. When you add an additional control axis to allow for the extension of the machine, you can connect it in a one-touch fashion using a bus cable.
Broad range of functional software "FBs" raises development efficiency.
Various software parts, FBs (function blocks), are available free of charge. By appropriately combining FBs, you can build a motion program for a large-scale system in a short time. If you have trouble in developing programs, consult Fuji for support.
Fuji Electric Alpha 7 example system configuration.
High-speed serial bus (compatible with SX bus) VS/LS Types.
You can easily build a highly functional motion control system that includes synchronous and interpolation control.
General-purpose interface VV-trype.
A single unit allows:
- Positioning run (immediate data operation) based on Modbus-RTU
- Positioning run (with 31 positioning data points) based on Di/Do signals
- Position, speed, and torque control run based on pulse train/analog input.
Open Network (with support for EtherCAT) VC-Type.
EtherCAT applications (with support for six different control modes and for synchronous (DC, SM2) and asynchronous (FreeRUN) modes).
Design and features.
Easily analyze the cause of alarm occurrence.
When an alarm occurs, the system displays the content of the alarm as well as related data such as the speed and torque at the time of alarm occurrence. This allows you to accurately analyze the cause of the alarm.
Life prediction and preventive maintenance features.
You can check the status of the servomotor from the controller, so you can perform maintenance at appropriate time. In addition, the system predicts the life for the following consumables and sends the data to the host controller for proactive failure prevention.
- Battery
- Main circuit capacitor
- Cooling fan
Long life design of servo amplifier parts.
The design life of long-life parts has been further extended: 10 years for electrolytic capacitors and cooling fans. In addition, the design life of the battery is approximately 35,000 hours. (Retention time with the power supply shut off)
- The use conditions are as follows.
- Ambient temperature: 30°C (annual average)
- Load factor: Up to 80%
- Rate of operation: Up to 20 hours/day
The environmentally resistant servo motor can be used in an environment with exposure to water and dust.
The servomotor is by default compliant with IP67* defined by the International Electrotechnical Commission (IEC). It has Class 6 dust resistance and Class 7 water resistance, which means that it can be used in an environment with exposure to water and dust.
*Except for shaft-through part (also except connectors for GYS and GYB motors of lead wire type).
Most compact in the industry* Further miniaturized servomotor.
The overall length of the servomotor has been reduced by approximately 15mm, compared with our existing products. This is the most advanced miniaturization in the industry.
* As of February 2017, for the GYB motor.
Compact servo amplifier that can be mounted in close contact.
The servo amplifier is reduced in width by 5mm and in footprint area by approximately 12%* when compared with our conventional model. It can be mounted in close contact, allowing the reduction of the space required to mount it on the control panel of the machine.
* When mounted in close contact, 80% ED rating applies.
There is no restriction when installed at spacings of 5mm or greater.
* Comparison value with frame 1.
The servo amplifiers can be mounted close together even when ABS backup batteries are installed. Batteries can be easily replaced while the servo amplifiers are mounted.
Various features that allow standalone use of Fuji Electric ALPHA 7.
Automatic servo adjustment in tuningless mode.
In tuningless mode, you do not have to manually adjust the responsiveness (gain) because the servo system automatically does so. You no longer spend time on tuning at start-up time.
Finer adjustment is possible in auto tuning mode.
In auto tuning mode, the servo amplifier automatically adjust the responsiveness (gain). This mode allows finer control than tuningless mode.
Highest precision requirements can be achieved in manual tuning mode.
This mode is intended for use with machines that require high precision. It allows you to optimize multiple parameters at once, enabling high responsiveness (gain) adjustment.
Evolved control functions contribute to streamlining of operation and stabilization of quality with Fuji Electric Alpha 7.
New damping control suppresses the vibration at equipment edges.
The introduction of a new control algorithm reduces the vibration at the edges of the equipment to one tenth, compared with the conventional damping control (used in our products). Support for models with three inertia systems makes it possible to control low-frequency vibrations at two points concurrently.
The interference detection feature detects a collision, etc. and prevents breakage.
The servo amplifier detects interference on the equipment (such as a collision with an edge of the machine) and operates to mitigate the shock to the machine when a collision occurs. This feature helps prevent damage to the equipment and reduce load on it.
* Protection may not be complete depending on the operation type.
The cogging feature ensures smooth operation.
Since interference due to cogging of the servomotor is detected and compensated, speed ripples due to cogging can be reduced and smooth operation can be ensured even if the equipment does not support the increase of the speed loop gain.
Maximum input pulse frequency of 4MHz.
The system can support input frequencies from the host controller until the maximum frequency of 4MHz is reached. This allows a finer amount of travel per pulse, thus enabling positioning operation at a higher precision than before.
- Differential input: Max. input frequency ≤ 4.0 [MHz]
- Open collector input: Max. input frequency ≤ 200 [kHz]
However, the VS type supports only the counter feature and it cannot support pulse train operation.
The notch filter feature suppresses the resonance of the machine.
Now five notch filters are incorporated instead of two, further improving the machine resonance suppression feature.
The motor status can be monitored from the host controller.
The system detects machine resonance and automatically configures the notch filters. While the auto notch filter feature is on, the system constantly performs detection and calculation, thus being able to respond even to moment-to-moment changes in resonant frequency.
One of three motor stop methods can be selected.
You can select "rapid deceleration stop", "DB stop", or "coast-to-stop" when an alarm occurs, when the main power is off, or when the servo-on signal is off. Since limiting output torque at desired value is possible even if rapid deceleration stop is selected, impact shock to the machine can be reduced.*
* However, it is enabled when the control power supply is input.
A homing program can be easily configured.
Several homing features allow simple configuration by just combining servo parameters.
Interrupt positioning feature (except for EtherCAT type).
You can easily perform positioning run, using pre-registered positioning data. You can register positioning data for up to 31 points in VV type and up to 99 points in LS type. You can run the system by just selecting a program number and issuing a start command from the host controller. This feature is most useful for the purposes of inching and repetitive operations.