Fuji Electric, Alpha 5 series servo system
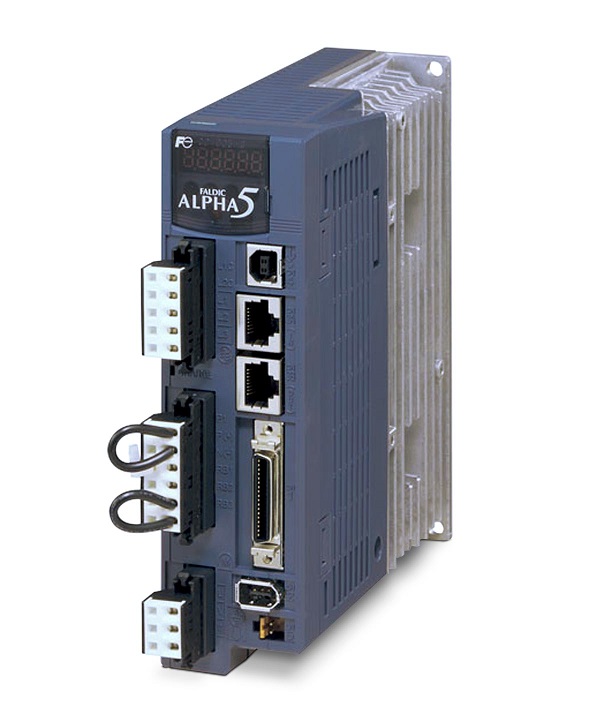
- Easy PTP Positioning: Position function is embedded as standard in general-purpose interface unit (VV type)
- Simple Connection: General purpose communication servo
- All kinds of general-purpose PLC, controller, or HMI (POD) applicable with Modbus-RTU can be connected to ALPHA5
- High Performance: High-speed, high-precision positioning
- Frequency response 1500 Hz
- Max motor speed 6000 r / min
- High-resolution encoder
- 18-bit ABS/INC 262,144 pulses
- 20-bit INC 1,048,576 pulses
Fuji Electric, Alpha 5 series servo system
Positioning function is embedded as standard in general purpose interface unit "ALPHA5 VV". As the ALPHA5 VV type is the standard model, external positioning unit or dedicated items for positioning are not required.
Following operations are enabled by one unit:
- Positioning via Modbus-RTU communications (immidiate value data)
- Positioning via Di/Do signal (positioning data 15 points*)
- Controlling positions, speeds and torques via pulse/analog input
Simple connection with Fuji Electric Alpha 5 series Modbus-RTU communications
Operations such as PTP positioning operation, parameter edit, and various monitoring are enabled. All you need to do is connect HMI (POD), general-purpose PLC, or PC controller directly to servo amplifier via Modbus-RTU communications.
Compatibility with SX bus: VS type and LS type.
Sophisticated motion control system that has synchronizationand interpolation controls can be configured easily.
Fast and accurate positioning is realized.
- New high speed servo control engine.
Frequency response 1500Hz.
- Increased motor rotation speed.
Max. rotation speed 6000r/min.
- Fine resolution encoder.
18-bit absolute 262,144 pulses.
20-bit incremental 1,048,576 pulses.
High performance frequency response (1500Hz), high rotation speed (6000r/min) and high resolution encoder reduce the cycle time and make faster and more accurate positioning and settling possible.
New control functions.
- New notch filter (auto notch filter).
The notch filter is set automatically upon detection of mechanical resonance. Because detection and calculation are always conducted while the auto notch filter remains turned on, resonance frequencies changing by time are effectively filtered.
- Homing by hit-to-stop.
Wire saving can be achieved with elimination of the limit switch and over travel signal. Moreover, several homing functions allows homing program creation to be simplified only by combining the servo parameters. Creating complicated program of homing in the host controller is no more necessary.
- Motor stop method setting is enabled.
Alarm occurrence.
Main power supply is OFF.
Servo ON signal is OFF.
Selection among rapid deceleration stop, DB stop, and coast-to-stop is enabled under the above conditions. Since limiting output torque at desired value is possible even if rapid deceleration stops is selected, impact shock to the machine can be reduced.