DOLD Reversing contactors POWERSWITCH
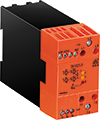
DOLD reversing contactors of the POWERSWITCH series are used to change the direction of rotation in alternating current motors, start them gently and/or to monitor their load. Various diagnostic functions inform you constantly about the operating condition of the motor. The DOLD reversing contactors save space and have few wires as all functions are combined in a single housing. Costs can also be saved as an alternative to a frequency converter. The devices are universally usable, e.g. for extruders, pumps, actuators or conveyors.
Type | Function | Load current [A], 3 pole | Load voltage, 3-phase AC [V] | Auxiliary voltage AC [V] | Digital triggering [V] | Temperature monitoring | Signalling output | Housing style: Width [mm] | ||
---|---|---|---|---|---|---|---|---|---|---|
DC | AC /DC | AC | ||||||||
BH 9253 | Standard | 3.6; 8.5; 11.5 | 24 ... 500 |
|
24 | 230 | 400 | + | + | Switch cabinet: 45; 67.5; 112.5 |
BH 9255 | with current monitoring | 3.6; 8.5; 11.5 | 24 ... 500 | 400 |
|
230 |
|
+ | + | Switch cabinet: 45; 67.5; 112.5 |
BI 9254 | with softstarting and active-power monitoring | 11.5 | 400 |
|
24 |
|
|
+ | + | Switch cabinet: 90 |
zero-voltage switching with integrated electrical interlock and heat sink, top hat rail mounting
Temperature sensing.
To protect the power semiconductors the unit incorporates temperature monitoring. When overtemperature is detected the power semiconductors swith off and an output relay as well as a red LED is activated. This state is stored. When the temperature is back to normal the semiconductors can be activated again by switching off and on the control voltage.
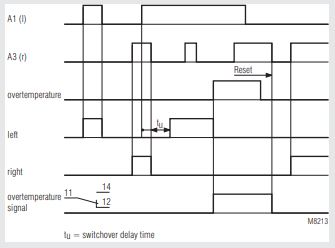
- According to IEC/EN 60 947-1, IEC/EN 60 947-4-2
- Switching at zero-crossing
- To reverse 3 phase asynchronuos motors up to 5.5 kW / 400 V (7.5 HP / 460 V)
- Electrical interlocking of both directions
- Temperature monitoring to protect the power semiconductors
- Measured nominal current up to 20 A
- LEDs for status indication
- Galvanic separation between control circuit and power circuit
- 45 mm; 67.5 mm; 112.5 mm width
- According to IEC/EN 60 947-1, IEC/EN 60 947-4-2
- Switching at zero crossing
- To reverse 3 phase asynchronuos motors up to 5.5 kW / 400 V (7.5 HP / 460 V)
- Electrical interlocking of both directions
- Temperature monitoring to protect the power semiconductors
- Measured nominal current up to 20 A
- LEDs for status indication
- Galvanic separation between control circuit and power circuit
- With current monitor
- 45 mm; 67.5 mm; 112.5 mm width
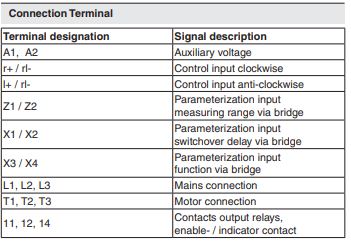
Without bridge x3-x4 (plc control).
After connecting the power supply to A1/A2 the enabling contact 11-14 closes. The motor is now started with a positive edge of the signal on control input r+/rl- (clockwise) or l+/rl- (anti-clockwise). The start up delay runs. If the start up delay is finished and the current is still over the adjusted value the relay contacts switch back to 11-12. This state is stored. It resets by switching off the motor on the control input. If the motor current rises above the adjusted value during operation the time tv (switching delay) runs down. If the switching delay is finished and the current is still over the adjusted value the relay contacts switch back to 11-12. This state is stored. It resets by switching off the motor on the control input.
With bridge x3-x4 (preferred for manual control).
Same function as without bridge, but in addition to the relay contact 11-12 also the motor is switched off at the same time.
Bridge x1-x2: Switchover delay tu 20 or 100 ms.
Temperature sensing.
To protect the power semiconductors the unit incorporates temperature monitoring. When overtemperature is detected e.g. because of reversing to often the power semiconductors swith off and an and the enabling relay switches back in position 11-12. This state is stored. When the temperature is back to normal the semiconductors can be activated again by switching off and on the control voltage.
- To reverse 3 phase motors
- Electrical interlocking of both directions
- 2-phase softstart
- Active power monitoring after softstart
- Temperature monitoring of power semiconductors
- LED indicator
- Internal auxiliary voltage are made from phase voltage
- Galvanic separation of control circuit and power circuit
- Space and cost saving with 3 functions in one compact unit
- Reducing of wiring and wiring failure
- Width 90 mm.
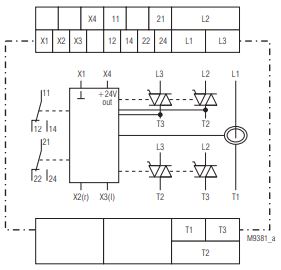
- Reversing operation for door and gate controls, bridge drives and lifting applications with monitoring of blockage
- Conveyor systems with monitoring of blockage
- Actuating drives in process controls with blockage monitoring
Function.
The reversing contactor BI 9254 is used to reverse the direction and to monitor the effective power on 3-phase asynchronous motors. An electrical interlock blocks the simultaneous control of both directions. To monitor the effective power correctly the current in the 3 phases has to be symmetric. The monitoring function only gets active after an adjustable start up delay. The 3 phases L1, L2 and L3 are connected continuously to the unit.
Temperature monitoring.
To protect the semiconductors their temperature is monitored. If overtemperature is detected, the power semiconductors switch off, the signalling relay 1 de-energises and the red LED flashes Code 1. This state is latched. After the temperature is back to normal the status can be reset by switching the control input on and off.
Softstart.
Two phases are controlled by thyristors in order to let the current rise slowly and to limit it. The motor torque reacts accordingly during start-up. This allows to reduce shock and stress for the mechanical parts of the drive. Start-up time and starting torque can be set with potentiometers.
Effective load measuring.
After an adjustable start up time, but at the earliest after end of ramp up time, the effective power of the connected motor is monitored. The effective power is defined as P = U x I x cosϕ. The maximum motor load is adjustable with potentiometer. A yellow LED indicates overload, but only as long as the motor is actually in overload state. After an adjustable time delay of 1…10 s a relay contact switches on until the effective load drops again under the adjusted value.
Control inputs.
With 2 control inputs left and right rotation is selected. When both inputs are activated the first signal will be accepted as valid. The inputs can be controlled by volt free contacts or with external DC 24 V. With activation of a control input the ramp up time and the start up delay is started again. The unit does not create any extra interlocking times for reversing operation except a short delay that is necessary to control the semiconductors. If one or both control inputs are active when applying auxiliary supply, a failure code “Control input active when unit switched on” is displayed. The Error LED flashes code 6. By disconnecting the control inputs the failure state is reset.
Monitoring relay 1 (contact 11-12-14).
The relay energises as soon as the unit is ready for operation after auxiliary supply is connected. On overtemperature, phase failure or wrong phase sequence the relay de-energises and the power semiconductor switches off.
Monitoring relay 2 (contact 21-22-24).
The relay energises, when after the adjusted time delay the effective power exceeds the setting value (energized on trip). The relay de-energises as soon as the effective power drops below the adjusted value. In the case of any other failure the relay de-energises.
Technical Information and Features
DOLD POWERSWITCH reversing contactor BH 9253 overview.
The reversing contactor BH 9253 is used to reverse the direction of 3-phase asynchronuos motors by switching 2 phases. An electrical interlokking disables the control of both directions at the same time. The reversing contactor has a short on and off delay time. When reversing the phases a switchover delay is guaranteed.Temperature sensing.
To protect the power semiconductors the unit incorporates temperature monitoring. When overtemperature is detected the power semiconductors swith off and an output relay as well as a red LED is activated. This state is stored. When the temperature is back to normal the semiconductors can be activated again by switching off and on the control voltage.
- According to IEC/EN 60 947-1, IEC/EN 60 947-4-2
- Switching at zero-crossing
- To reverse 3 phase asynchronuos motors up to 5.5 kW / 400 V (7.5 HP / 460 V)
- Electrical interlocking of both directions
- Temperature monitoring to protect the power semiconductors
- Measured nominal current up to 20 A
- LEDs for status indication
- Galvanic separation between control circuit and power circuit
- 45 mm; 67.5 mm; 112.5 mm width
DOLD POWERSWITCH reversing contactor with current monitor BH 9255 overview.
The reversing contactor BH 9255 is used to reverse the direction of 3-phase asynchronuos motors by switching 2 phases (L1 and L2). An electrical interlocking disables the control of both directions at the same time. The reversing contactor has a short on and off delay time. When reversing the phases a switchover delay is guaranteed. The motor current is monitored in phase L1. If the current rises above the tripping value the device is able to switch off the motor.- According to IEC/EN 60 947-1, IEC/EN 60 947-4-2
- Switching at zero crossing
- To reverse 3 phase asynchronuos motors up to 5.5 kW / 400 V (7.5 HP / 460 V)
- Electrical interlocking of both directions
- Temperature monitoring to protect the power semiconductors
- Measured nominal current up to 20 A
- LEDs for status indication
- Galvanic separation between control circuit and power circuit
- With current monitor
- 45 mm; 67.5 mm; 112.5 mm width
Without bridge x3-x4 (plc control).
After connecting the power supply to A1/A2 the enabling contact 11-14 closes. The motor is now started with a positive edge of the signal on control input r+/rl- (clockwise) or l+/rl- (anti-clockwise). The start up delay runs. If the start up delay is finished and the current is still over the adjusted value the relay contacts switch back to 11-12. This state is stored. It resets by switching off the motor on the control input. If the motor current rises above the adjusted value during operation the time tv (switching delay) runs down. If the switching delay is finished and the current is still over the adjusted value the relay contacts switch back to 11-12. This state is stored. It resets by switching off the motor on the control input.
With bridge x3-x4 (preferred for manual control).
Same function as without bridge, but in addition to the relay contact 11-12 also the motor is switched off at the same time.
Bridge x1-x2: Switchover delay tu 20 or 100 ms.
Temperature sensing.
To protect the power semiconductors the unit incorporates temperature monitoring. When overtemperature is detected e.g. because of reversing to often the power semiconductors swith off and an and the enabling relay switches back in position 11-12. This state is stored. When the temperature is back to normal the semiconductors can be activated again by switching off and on the control voltage.
DOLD POWERSWITCH reversing contactor with softstart and active power monitoring BI 9254.
- According to IEC/EN 60 947-1, IEC/EN 60 947-4-2- To reverse 3 phase motors
- Electrical interlocking of both directions
- 2-phase softstart
- Active power monitoring after softstart
- Temperature monitoring of power semiconductors
- LED indicator
- Internal auxiliary voltage are made from phase voltage
- Galvanic separation of control circuit and power circuit
- Space and cost saving with 3 functions in one compact unit
- Reducing of wiring and wiring failure
- Width 90 mm.
- Reversing operation for door and gate controls, bridge drives and lifting applications with monitoring of blockage
- Conveyor systems with monitoring of blockage
- Actuating drives in process controls with blockage monitoring
Function.
The reversing contactor BI 9254 is used to reverse the direction and to monitor the effective power on 3-phase asynchronous motors. An electrical interlock blocks the simultaneous control of both directions. To monitor the effective power correctly the current in the 3 phases has to be symmetric. The monitoring function only gets active after an adjustable start up delay. The 3 phases L1, L2 and L3 are connected continuously to the unit.
Temperature monitoring.
To protect the semiconductors their temperature is monitored. If overtemperature is detected, the power semiconductors switch off, the signalling relay 1 de-energises and the red LED flashes Code 1. This state is latched. After the temperature is back to normal the status can be reset by switching the control input on and off.
Softstart.
Two phases are controlled by thyristors in order to let the current rise slowly and to limit it. The motor torque reacts accordingly during start-up. This allows to reduce shock and stress for the mechanical parts of the drive. Start-up time and starting torque can be set with potentiometers.
Effective load measuring.
After an adjustable start up time, but at the earliest after end of ramp up time, the effective power of the connected motor is monitored. The effective power is defined as P = U x I x cosϕ. The maximum motor load is adjustable with potentiometer. A yellow LED indicates overload, but only as long as the motor is actually in overload state. After an adjustable time delay of 1…10 s a relay contact switches on until the effective load drops again under the adjusted value.
Control inputs.
With 2 control inputs left and right rotation is selected. When both inputs are activated the first signal will be accepted as valid. The inputs can be controlled by volt free contacts or with external DC 24 V. With activation of a control input the ramp up time and the start up delay is started again. The unit does not create any extra interlocking times for reversing operation except a short delay that is necessary to control the semiconductors. If one or both control inputs are active when applying auxiliary supply, a failure code “Control input active when unit switched on” is displayed. The Error LED flashes code 6. By disconnecting the control inputs the failure state is reset.
Monitoring relay 1 (contact 11-12-14).
The relay energises as soon as the unit is ready for operation after auxiliary supply is connected. On overtemperature, phase failure or wrong phase sequence the relay de-energises and the power semiconductor switches off.
Monitoring relay 2 (contact 21-22-24).
The relay energises, when after the adjusted time delay the effective power exceeds the setting value (energized on trip). The relay de-energises as soon as the effective power drops below the adjusted value. In the case of any other failure the relay de-energises.